A Complex and High-Tech Restoration
This was a restoration that took hundreds of hours from the Atelier’s professionals and serves as a prime example of how we apply the same care and technique to instruments belonging to top-tier professional musicians (such as Marc Johnson’s double bass featured on the website) as we do to those of semi-professionals, amateurs, or students, as in the case of this instrument.
Every instrument deserves the same level of care, as they pass from hand to hand and are not always fortunate enough to have a careful owner for long.
This page includes 81 photos and showcases some of the techniques employed in our Atelier.
The project required the use of advanced techniques, dozens of molds made from plaster, alginate, acrylic, and, most notably, wood, resulting in a high-level restoration. The instrument was in poor condition, with square and rectangular holes in the ribs, a poorly executed triangular patch on the back, among many other issues. Follow below for a high-level restoration.



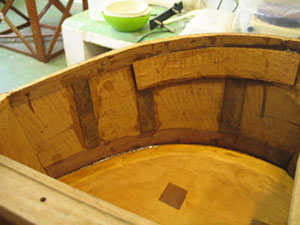
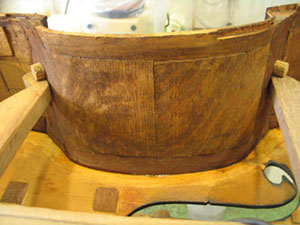
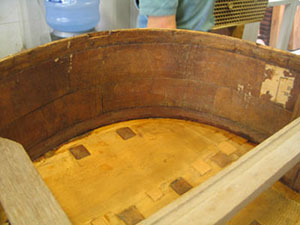
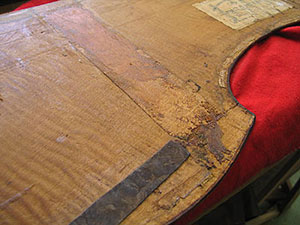

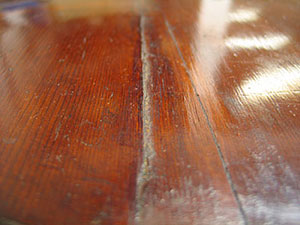
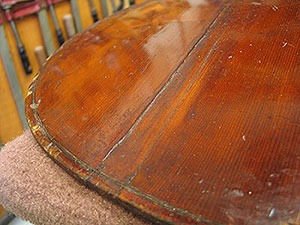
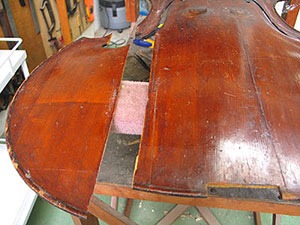

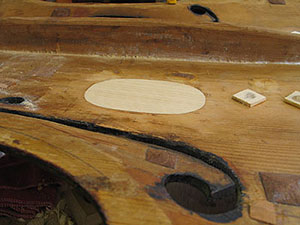

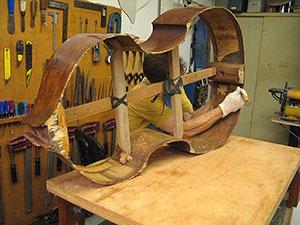
This was the state of the instrument, which was completely disassembled.
All the old and deteriorated glue was removed and the bass was completely disassembled and glued back together.
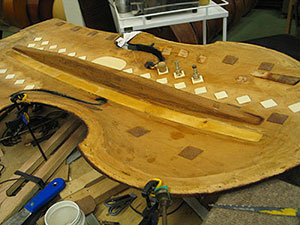

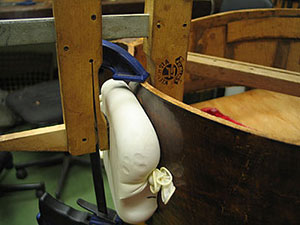
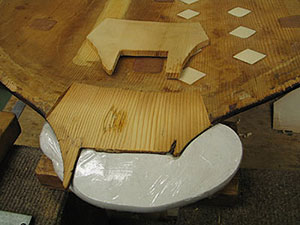
More than 450 photos were taken during the months of restoration of the instrument and we have included here only 81 that show certain phases of the work.
Above you can see a square hole in one of the instrument’s ribs, one of the absurd patches we found.
For this restoration, 12 plaster and/or alginate molds were made.




The back is getting a new bar, and the bass bar is being glued to the top.
No old joists or reinforcements are left. They were all poorly made or already useless.
Dozens of grafts were made, using the same type of wood and with the same type of color, age, and grain of the original wood.
Before, in these places and many others, there was a dried-out mass.

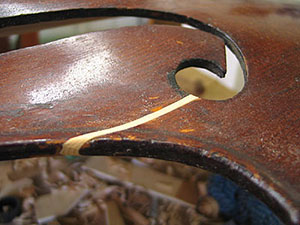
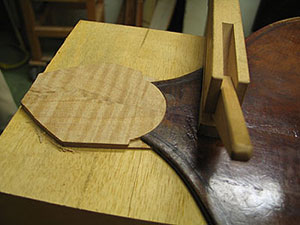



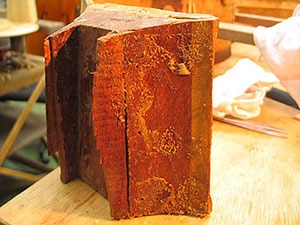
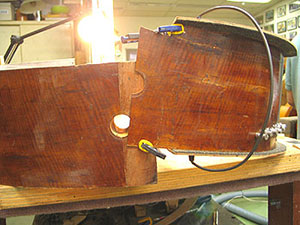
Button reinforcement, dozens of cracks in the ribs, the new bass bar already glued, and a new upper block being made.
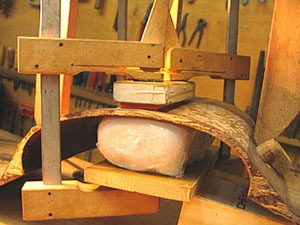

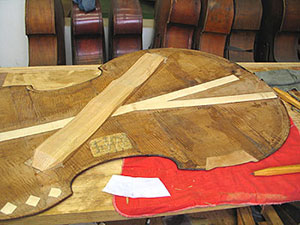

A crack being cleaned of old glue using a very soft brush.
This work took dozens of hours because the wood could not be damaged, only to remove the already deteriorated but adhered glue, and dozens of cracks were reopened and glued again at the level and using the appropriate techniques.


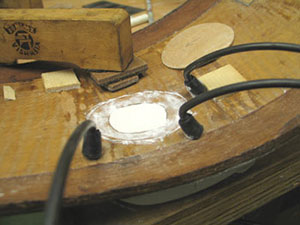

The back is almost finished, with more plaster molds and a square hole in one of the ribs being restored. A plaster bed was made for this point, as seen above.
The area was worked on internally, keeping as much of the original material as possible but leaving enough gluing area for effective work.
A new piece was made using the same type of wood and with the same characteristics as the original.



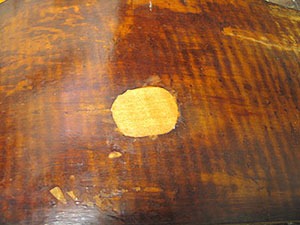
Using the plaster bed, the perfectly fitting graft was glued to the rib.
Remember that a double bass rib is less than 3mm thick and this work is very delicate.
The rib prepared to be molded and the graft ready after drying, which takes a few days, as there is no air inside the pressing to dry quickly.
Many gluings on this instrument took days to dry.

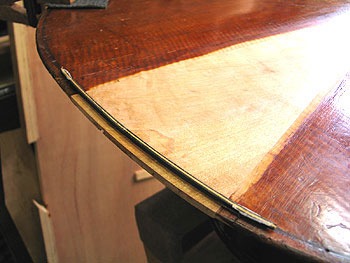
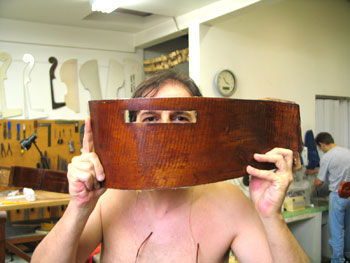
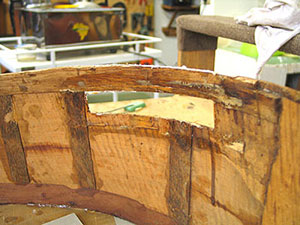
Purfling restoration. This was done on several parts of the bass.
It was necessary to make purfling with exactly the same thickness as the original for this job.
Watch the restoration of a rectangular hole in another rib.
See the terrible condition this instrument was in and how it has transformed into something clean and correct over time.

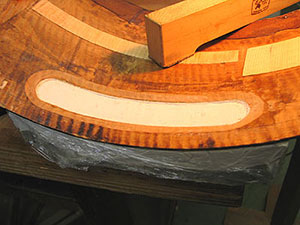
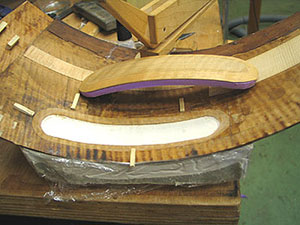
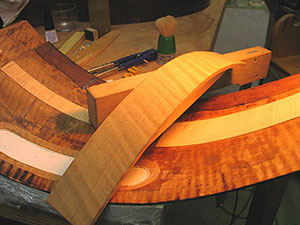
More plaster beds, more work on the rib, keeping as much of the original material as possible, more wooden molds and a maple graft, exactly like the original.
And time passed.

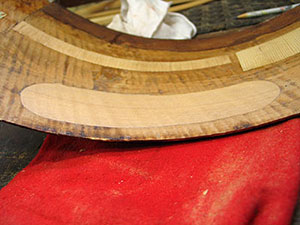
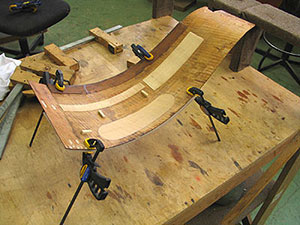
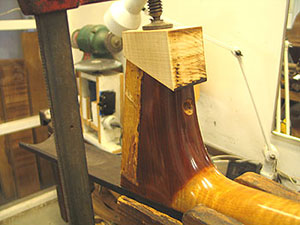
The glue had already dried, days later, both internally and externally.
In the end, the thickness of the rib remained the same as the original.
The neck, like the rest of the instrument, also had problems with position and angle, as well as a hole for a huge screw that was removed with great effort.

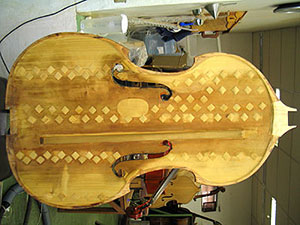
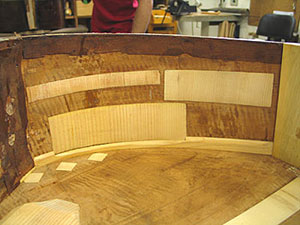

The back is already finished and glued to the ribs, which are also finished, and the top is also ready.

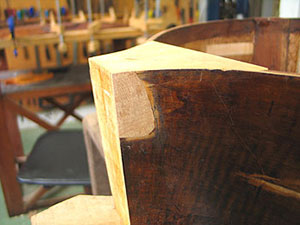

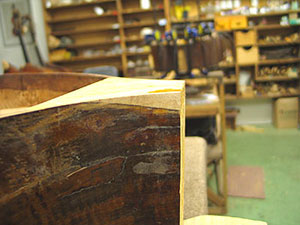




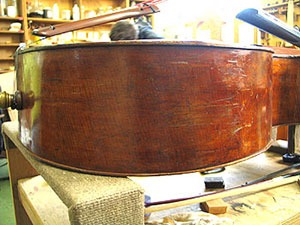
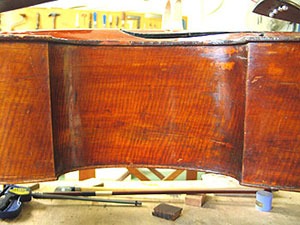
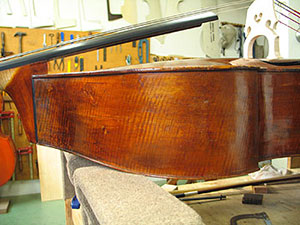
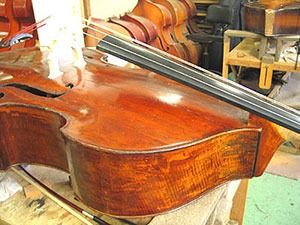
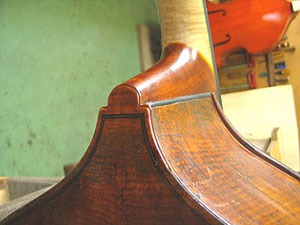


It is very difficult to see where the square holes, the triangular patch, the poorly made patches and masses were before.
A job that made everyone involved in it very proud.

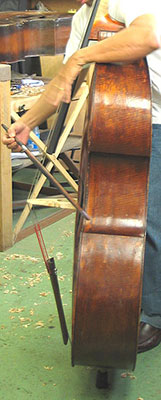
The bass presented a very balanced and powerful sound in all registers, giving very high levels of attack and sustain in acoustic tests.

Unfortunately, at the time, the owner of the double bass was unable to properly value the work carried out by several luthiers over many weeks or to acknowledge the improvements made to the instrument, attempting to evade their obligations. However, this does not change our approach in any way.
Our duty is always to the instrument.
In time (it may take a few decades, but it always happens), this instrument will be in other hands and, with luck, with a professional who deserves it.
This instrument, like all others, had a history before us and will have a history after us.
The life of a double bass far exceeds that of a human being, unless a very serious accident occurs.
Just looking at the photos and recalling the challenges overcome, the teamwork accomplished, and the fantastic final result brings us pleasure, pride, and reward.
Recognition comes from those who have it to give.
Making – Restoration
Maintenance – Rent
Evaluation – Buying and Selling
Specialized in Double Basses since 1980
Rua Marselhesa 387 – Vila Mariana – SP
Monday to Friday from 10 am to 5 pm
By appointment only
We send only ONE email each month with instruments for sale and new products.
Subscribe below to be added to the list.
© Copyright – 2021 – Paulo Gomes – All rights reserved